Implant screw mechanics
The screw joint consists of the two parts tightened together by a screw, such as an abutment and an implant being held together by a screw. The interplay of screw joint separating forces (external) and clamping forces (internal) affect screw joint stability. The screw loosens when the separating forces are greater than the clamping forces. To achieve secure rigid joint assembly, the clamping force should be greater than the separating forces.The initial clamping force is achieved with the tightening of the screw and is proportional to the tightening torque. Small torque does not achieve joint stability and large torque leads to screw fatigue or stripping of screws . The contact force, the initial tension on the screw, clamps together the assembly components of the screw joint is known as the preload (explained below) (Fig. 4). These forces are generated within the screw when torqued. The tightening torque is applied to the head of the abutment screw as a moment, transformed along the interface of the screw thread surfaces and the implant threaded surfaces. The tensile forces forming within the screw stretches the screw causing frictional forces to develop between the engaging threads leading to compressive forces building up and securing the joint parts tightly against each other .
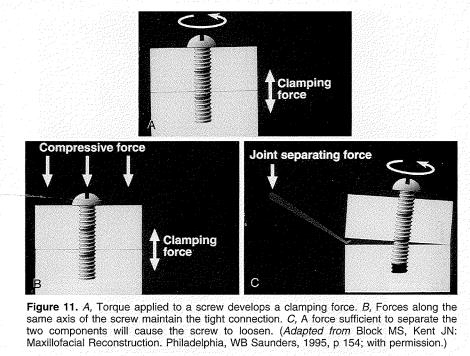
Figure 4. Clamping forces.
Preload
Preload is the tension created in a screw, especially in the fluked threadings, when tightened. Preload is the contact force that clamps the abutment and the implant as that tightening torque is increased above the initial contact. The optimum preload force recommended for any implant screw is 75% of the yield strength of the abutment screw. Preload is not only affected by the amount of torque applied but also the design of the screw. The threads of the screw and the internal threads of the implant cannot be machined smooth perfectly. The only contacting surfaces are the high spots when the initial torque is applied. That leads to the development of preload. These high spots wear with under loading and 2-10% of the initial preload will be lost. This is a mechanical engineering principle known as embedment relaxation. The amount of embedment relaxation is dependant on the roughness of the surface of threads, the surface hardness of the materials and the amount of load subjected.